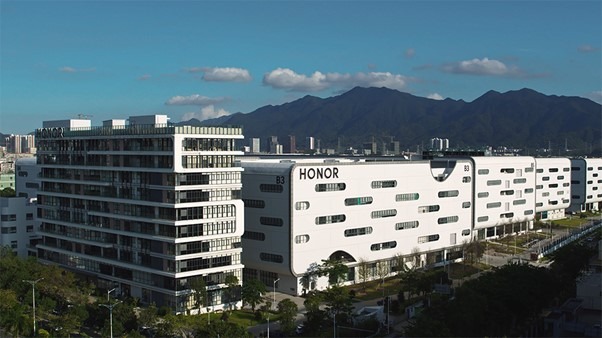
HONOR has today debuted its HONOR Intelligent Manufacturing Industrial Park, the brand’s first self-funded factory. The Park will handle certification of new product quality control, production of flagship devices, new craftsmanship and technology incubations, and building HONOR’s artificial intelligence manufacturing capacities. Through its industry-leading innovations, quality control capabilities and global supply chain partners, HONOR is confident this new facility will support its goal to provide premium products and best-in-class user experiences to global consumers.
“As a premium technology product provider, being able to ensure our standards of reliability and quality will be paramount as we continue our journey to become a leading global technology brand,” said George Zhao, CEO of HONOR Device Co. Ltd. “We are proud to announce the opening of our new manufacturing facility which will be integral to assuring our wider range of premium products are of the highest quality.”
Managing End-to-End Quality Control with the Power of Automation and Intelligence
Automation reduces the variation and defects caused by human errors resulting in greater consistency in quality. HONOR’s Intelligent Manufacturing Industrial Park is equipped with industry-leading high precision automatic manufacturing technology, including an automatic precision assembly machine (for installing the 89° Super Curved Display used in HONOR smartphones) that can achieve assembly precision of up to 75 microns (about a hair’s diameter). The automatic battery assembly equipment adopts high-precision optical detection which can detect foreign bodies (as small as up to 40 microns) and monitor real-time pressure, ensuring the safety of batteries produced and reducing safety risks caused by manual work. Seventy-five per cent of the production line is completed using automation, of which more than 40 per cent was developed by HONOR’s own Research & Development team. HONOR’s automated production line enables one smartphone to leave the line every 28.5 seconds (cycle time).
Quality control is ensured from the manufacturing to the testing phase through the close monitoring of every step of the assembly line. When an anomaly is detected, an alert is triggered followed by timely correction of the issue. While the common industry practise is to separate assembly and burn-in testing (offline ageing process), HONOR uses an online ageing process where assembly and burn-in testing are done in one process. HONOR’s process consists of over 150 prediction tests that quickly detect quality issues and shorten the turnover and testing period.
HONOR has adopted the “manufacturing supermarket” concept to build a lean and intelligent material distribution system. The real-time demand of the production line is linked to the intelligent selection of off-shelf components. As a result, colleagues can manage a rapid error-free process of material selection that is then automatically delivered to the production station by Automated Guided Vehicles (AGV) across floors and inventory areas. After product packaging is completed, the AGV’s intelligent scheduling system automatically picks up the products.
Creating Premium Products that Go Beyond Industry Standards
After a thorough review of industry standards, certification standards and operator requirements, HONOR created its own quality standards to meet the range of international policies around the world. The company has over 600 quality standards, covering design, development, materials, manufacturing and user experience.
The HONOR Intelligent Manufacturing Industrial Park has industry-leading laboratories, including a reliability laboratory, regulatory laboratory and environmental protection laboratory. This combination of laboratories covers both material and product controls. The Park conducts nearly 200 stringent tests on all incoming materials prior to production and dozens of product tests postproduction. The inspection scope and frequency go beyond the usual industry practices to ensure HONOR’s products meet the stringent standards it has set for itself.
Promoting a Culture that Values Constant Improvement and Craftsmanship
Ensuring high quality requires constant and continuous improvements and the commitment of all employees. HONOR provides comprehensive employee training and promotes a culture that values continuous improvements. HONOR also adopts a “quality first, experience wins” strategy in all areas and fields.
HONOR has established a quality inspector system where inspectors representing customers perform unboxing inspections to check if there are any product anomalies. In addition, instead of the random selection inspection that is commonly used in the industry, HONOR adapts a precise sampling system where products with potential flaws are locked down and thoroughly inspected by its quality inspectors. HONOR’s quality inspectors have very strict, zero-defect standards to ensure customers do not receive flawed products.
The Park will serve as an incubator for HONOR’s next generation of manufacturing capabilities, showcasing the company’s abilities to deliver products of the highest level of quality and craftsmanship. Through all these efforts, HONOR hopes to contribute to the advancement of the entire industry and create consistent, high-quality products and ultimate experiences for consumers.